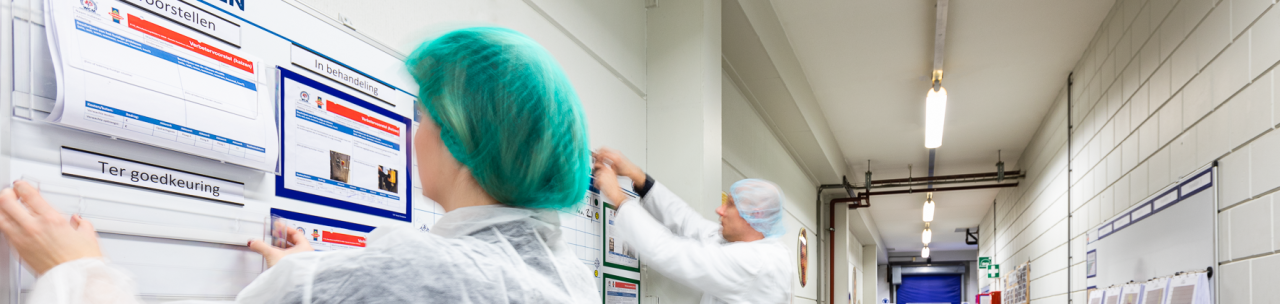
World Class Manufacturing (WCM)
BIJ DAELMANS BANKET B.V. | MET FLORIS WISKIE (WCM FACILITATOR) | 02-2022
Daelmans Banket B.V., al sinds 1904 genieten mensen van hun banketproducten. Een modern, internationaal en zelfstandig familiebedrijf dat vooral bekend staat om zijn Oer-Hollandse stroopwafel, waar het wereldwijd marktleider in is. Het levert ook producten als kokosbanket en speculaasbrokken. Dat produceren doen ze niet alleen onder het eigen Daelmans-merk, maar ook voor tientallen nationale en internationale private labels. Met ruim 200 medewerkers wordt inploegen gewerkt, verdeelt over 3 productielocaties.
Voor deze case mocht collega Stefanie van den Hoogen (als Project Manager) in gesprek met Floris Wiskie, WCM Facilitator over de 3 vestigingen van Daelmans. Floris is sinds 2015 werkzaam en is doorgegroeid vanuit de operatie tot interne WCM consultant. Samen met een collega heeft hij een uniek Daelmans-TPM-programma opgezet: WCM. Dit staat voor World Class Manufacturing. Het wordt pragmatisch en met een dosis ervaring ingevoerd.
WCM Programma
Bij Daelmans focussen ze zich op 3 pijlers: standaardisatie, verbeteren en inzicht. "Door standaarden vast te leggen worden afwijkingen zichtbaar en kun je op basis daarvan verbeteren," vertelt Floris.
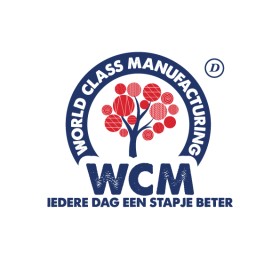
5S
Het standaardiseren van werkplekken en processen met 5S werkplekorganisatie.
Continu Verbeteren
Een Continu Verbetercultuur opzetten door te verbeteren op basis van zichtbare afwijkingen.
OEE
Het registreren en inzetten van de Overall Equipment Effectiveness (OEE) biedt waardevolle inzichten van waaruit verbeterd kan worden.
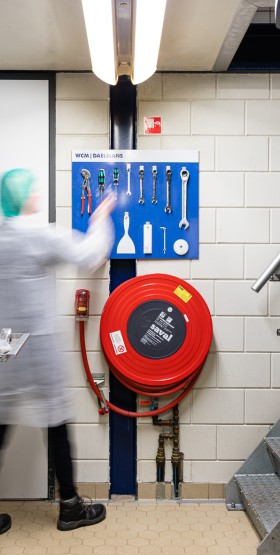
5S Werkplekorganisatie
De 5S'en: Scheiden, Schikken, Schoonmaken, Standaardiseren en Standhouden. Of zoals Daelmans het noemt: Stimuleren.
“Ons doel rondom het introduceren van 5S was vooral om een prettige werkomgeving te creëren. Maar ook om onnodige productiestilstanden te voorkomen.”
Floris geeft aan dat de werkplekken voorheen rommelig waren, wat onder andere resulteerde in lang zoeken naar de juiste gereedschappen en schoonmaakmaterialen. “Toch zag niet iedereen direct het nut in van een 5S-werkplek. Logisch dat je het kritisch bekijkt, als je al jaren op dezelfde wijze werkt,” vertelt Floris. “Het overtuigen van mensen in belangrijke functies is essentieel. Bij Daelmans zijn dat verreweg de teamleiders. Zij zijn dan ook als eerste getraind op 5S.”
Door het aanstellen van 5S-teams, bestaande uit teamleiders en ambassadeurs, ontstond er draagvlak. Uiteindelijk werd het hele productieteam getraind. Wel bleek niet alleen theoretische kennis noodzakelijk, maar ook absoluut overtuiging en een zichtbaar 'voorbeeldige' werkvloer voor het referentiekader.
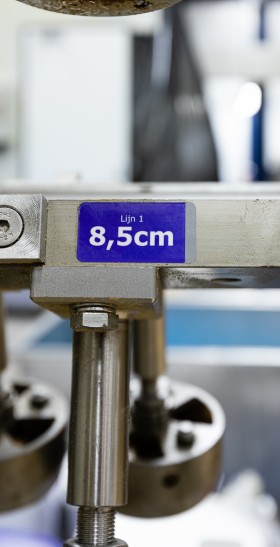
Schikken en locaties bepalen
De eerste stap werd gemaakt; het scheiden van nuttige en overbodige materialen. Opvolgend aan deze stap start schikken. Hierbij is aan medewerkers gevraagd een materiaallijst in te vullen. Welke gereedschappen en schoonmaakitems heb je op je werkplek echt nodig? Een lastige vraag, maar door kritisch te zijn houd je de tools over welke op je werkplek mogen blijven. Aan de hand van deze tools zijn gereedschaps- en schaduwborden ontwikkeld.
Floris: "Het voordeel van een gereedschaps- en/of schaduwbord is dat mensen snel inzichtelijk hebben of de materialen compleet zijn."
"Dit inzicht werkt heel efficiënt tijdens het werk en een ploegenoverdacht."
Kleurcodering
Ook machineonderdelen hebben door middel van kleurcoderingen extra locatiebepalingen gekregen. De items zijn gemarkeerd met stickers, zodat de mensen op de werkvloer snel kunnen matchen op kleur waar de items teruggehangen dienen te worden. Simpel maar doeltreffend.
Verbeteren met Kaizen
“Naast het standaardiseren willen we ook graag zien dat de werkstandaarden verbeterd worden. Verbeterideeën voor deze werkstandaarden worden vaak geopperd door operators en problemen komen voort uit OEE-registraties. Deze verbeterideeën hoe groot of klein ze ook zijn, verdienen aandacht en dienen besproken te worden. Om dit visueel te ondersteunen is er één verbeterbord per fabriek opgehangen. Dit bord hangt in een ruimte waar iedereen dagelijks passeert”, vertelt Floris.
Het verbeterproces pakken ze als volgt aan bij Daelmans: elke medewerker kan een verbetervoorstel of idee indienen. De overige teamleden moeten tekenen voor akkoord, voordat deze wordt doorgezet tot actie. "Op het formulier vragen we om een inschatting van de kosten versus de opbrengsten. Wekelijks bespreekt het Kaizen Team, met daarin de Plant Manager, Productieleiders en mensen van de Technische Dienst, in dertig minuten welke vier ideeën worden opgepakt. Ook de ideeën die niet uitgevoerd kunnen worden, worden teruggekoppeld aan de indiener waarom niet." Daelmans maakt dit proces inzichtelijk door de stappen nieuw voorstel, goedgekeurde voorstellen, afgekeurde voorstellen en succesvolle verbeteracties.
"Doordat er maar één verbeterbord in de gehele fabriek hangt, is er maar ruimte voor vier Kaizens tegelijk. Het lijkt weinig, maar het zorgt voor een korte doorlooptijd en snel resultaat. Dit alles motiveert en zorgt voor een gezonde stroom aan nieuwe verbeterideeën. Dit doordat medewerkers letterlijk zien dat zaken nu ook afgerond en opgevolgd worden."
Continu.
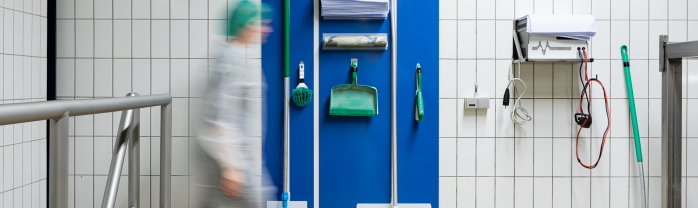